Why Every Workplace Needs First Aid Training at Work
Ensuring the health and safety of employees is a top priority for any business. One of the most critical components of workplace safety is first aid training at work. Accidents and medical emergencies can happen unexpectedly, and having employees trained in first aid is essential for reducing injury severity, preventing long-term health complications, and ultimately saving lives. In this blog, we’ll discuss the importance of first aid training at work, why every business should offer it, and the benefits of implementing this essential training.
What is First Aid Training at Work?
First aid training at work teaches employees how to recognise and respond to medical emergencies in the workplace. It equips them with the skills to manage various health situations, such as cuts, burns, fractures, and more serious conditions like heart attacks or strokes. This training covers essential life-saving techniques, such as CPR, wound care, and how to assist someone who is choking or unconscious.
By investing in first aid at work training, businesses ensure that their workforce is equipped to handle a range of medical emergencies, keeping both employees and the organization safe.
The Importance of First Aid Training at Work
Quick Response to Medical Emergencies
In an emergency, the first few minutes are crucial. First aid training teaches employees to recognise the signs of a medical emergency and provide immediate care, minimising the impact of the situation. The quicker an employee receives treatment, the better the chances of a full recovery.
Reduces Severity of Injuries
Proper first aid can reduce the severity of injuries, preventing long-term complications. By providing first aid training at work, employers ensure that workers can manage injuries effectively, reducing the chances of long-term harm.
Meets Legal Requirements and Compliance
In the UK, the Health and Safety Executive
(HSE) requires employers to provide first aid training in accordance with the size of the workforce and the nature of the business. Businesses must have sufficient first aid cover and a designated first aider to ensure compliance with Health and Safety regulations.
Training employees in first aid at work also demonstrates a business’s commitment to meeting regulatory standards, thus avoiding potential legal consequences.
Enhances Employee Confidence and Morale
When employees know that their colleagues are trained to handle medical emergencies, they feel more secure and confident in their work environment. This sense of safety leads to better morale and improved overall job satisfaction. Employees who feel cared for are more likely to remain loyal to their employer, reducing turnover and creating a positive company culture.
Cost-Effective and Preventative Measure
The cost of first aid training at work is minimal compared to the potential costs of workplace injuries. By investing in first aid courses, businesses can reduce the likelihood of serious injuries and avoid the long-term medical expenses and lost productivity associated with unaddressed medical emergencies. Additionally, a well-trained workforce can help lower workers' compensation claims, thus reducing insurance premiums.
Benefits of First Aid Training at Work
- Faster Medical Intervention: First aid-trained employees can take immediate action to stabilize the injured or ill person.
- Better Workplace Safety: Well-trained employees can prevent injuries from escalating and act as a deterrent to workplace accidents.
- Compliance with Health and Safety Laws: Providing first aid training ensures you meet legal requirements and avoid penalties.
- Boosts Employee Well-being: Employees who feel safe and cared for are more engaged and productive at work.
- Improved Workplace Culture: Training employees to respond effectively to emergencies creates a caring, supportive environment.
Why First Aid Training Matters:
First aid training at work is an essential investment for any business, regardless of industry. It provides employees with the knowledge and confidence to manage medical emergencies, helping to prevent the escalation of injuries and potentially saving lives. Additionally, it ensures that your workplace meets Health and Safety regulations, reduces the likelihood of long-term health complications, and promotes a positive, safe work environment.
At Sabretec Training, we offer comprehensive first aid at work courses tailored to the specific needs of your business. Our accredited first aid training services equip your workforce with the skills they need to act quickly and effectively during medical emergencies. Get in contact
with our expert team for more information on our range of courses available.
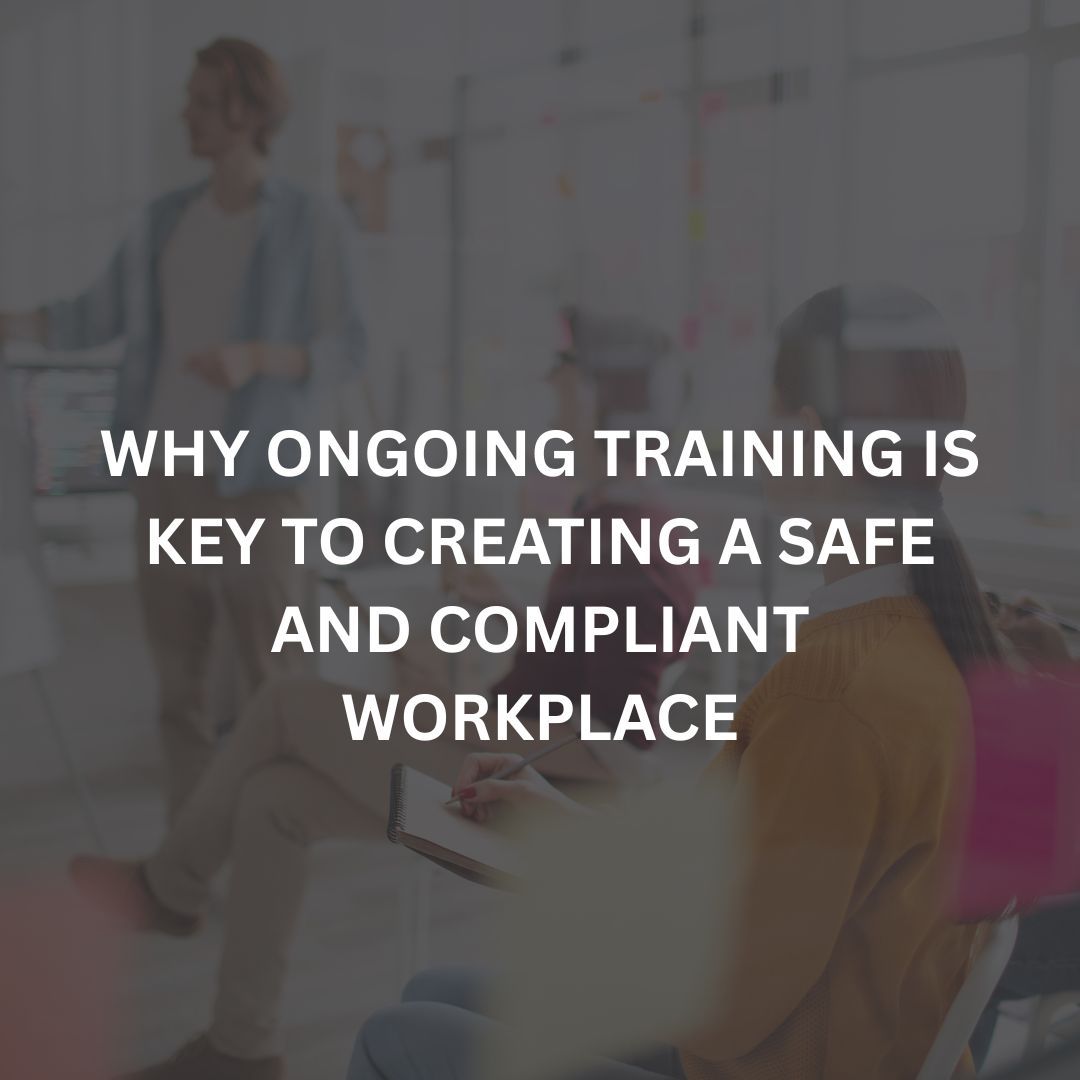
Creating a safe and compliant workplace is a long-term investment in your team. Regulations change, new risks emerge, and staff come and go. That’s why ongoing training is essential for maintaining safety standards and keeping your organisation fully compliant with current legislation. We support businesses across the UK with practical, flexible training solutions that meet the demands of today’s working environments. Safety conscious: Accidents in the workplace often stem from outdated knowledge or a lapse in routine. Providing regular training helps reinforce best practices and reduces the likelihood of injury or non-compliance. For example, Manual Handling Training refreshes employees on safe lifting methods and posture, lowering the risk of injury. Similarly, Forklift Training, when renewed periodically, ensures operators remain competent and confident in safely using equipment in line with industry expectations. Staying compliant Under UK health and safety law, employers must provide proper training to help their staff work safely. This includes everything from First Aid at Work courses to equipment handling and safety procedures. Keeping training up to date helps ensure you remain compliant with legislation such as the Health and Safety at Work Act and the Provision and Use of Work Equipment Regulations (PUWER). Beyond compliance, this demonstrates a clear commitment to your team’s wellbeing. Responding to change and risk Workplaces evolve over time with new equipment, expanded operations, and layout changes, these all introduce new hazards. Regular training enables your workforce to adjust and respond effectively. For instance, ongoing first aid training ensures staff are ready to manage medical incidents confidently, while refresher forklift training helps operators stay safe as working conditions or regulations shift. Partner with Sabretec Training With over 45 years’ experience in health and safety training, Sabretec Training delivers courses that are practical, recognised, and tailored to your business. We provide nationwide training on-site or off-site covering everything from first aid to manual handling and materials handling equipment (MHE). Contact Sabretec Training today for expert guidance and more information on our training courses.
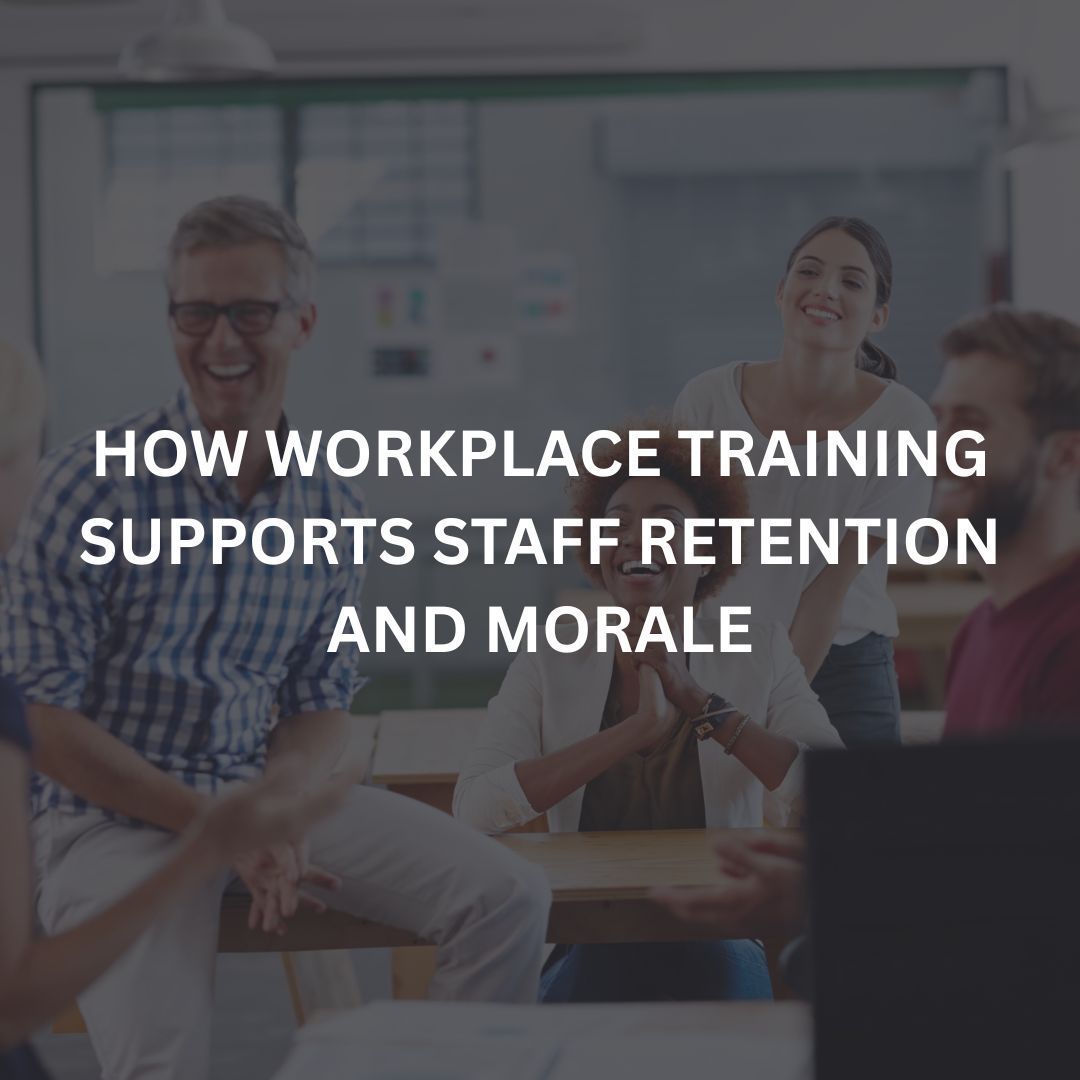
Retaining talented employees is a key priority for many businesses, and one of the most effective ways to achieve this is through ongoing workplace training. Providing staff with access to professional development not only improves safety and performance but also contributes significantly to employee morale and job satisfaction. At Sabretec Training, we help businesses across the UK deliver accredited, high-quality training that strengthens teams and supports long-term success. 1. Investing in Employees Builds Loyalty Offering courses such as First Aid at Work, Manual Handling, and Forklift Training sends a clear message, you value your team’s wellbeing and development. When staff see that their employer is committed to their growth and safety, they’re more likely to remain loyal and motivated, helping reduce turnover and recruitment costs. 2. Skilled Staff Are More Confident Training provides employees with the knowledge and confidence they need to work safely and effectively. Whether they’re operating machinery or handling an emergency, staff who have received proper training are more comfortable in their roles, leading to improved morale and a stronger workplace culture. 3. Supporting Development Encourages Progression Our verified and accredited courses offer staff tangible qualifications they can use to build their careers. This commitment to development boosts job satisfaction and signals to your team that they have a future with your company. 4. A Safe Workplace Promotes Positive Culture Proper training ensures a safer work environment, which helps build trust across your workforce. Fewer incidents mean less stress, reduced downtime, and a more positive day-to-day experience for your staff. Sabretec Training’s expert-led courses help businesses create compliant, secure workplaces where people feel protected and supported. 5. Choose Sabretec Training for Trusted, Flexible Solutions With over 45 years’ experience in the training industry, Sabretec Training offers tailored, compliant solutions for businesses of all sizes. We provide nationwide coverage, flexible scheduling, and a wide range of essential workplace training services to meet your needs. Get in touch with Sabretec Training to learn more about our workplace training options.